How to Produce Bamboo Flooring
Solid bamboo flooring is the first edition of Bamboo flooring invented 30 years ago, and it is a popular choice for many homeowners due to its durability, ease of installation, and environmental sustainability. It is so cool to transform a bamboo to the flooring, very amazing manufacturing process. Here is a full production step that you might never see it before, it is a very detailed display in words and pictures.
Harvesting and Cutting:
Bamboo used for flooring is typically harvested from managed forests when it reaches maturity, around 4-6 years. Cut 7-meter-long bamboo into predetermined lengths, if the flooring plank is 960mm in length, then the each cut should be 1010mm length to leave enough length to production.Splitting:
The bamboo stalks undergo a slicing process where they're cut into thin, flat strips. With thickness of 8mm.Removing Green and Yellow Layers:
Remove the outer green layer and the inner yellow layer, or it will severely affect the adhesive strength; the tolerance of the bamboo strip thickness and width should be controlled within 0.1mm.Boiling and Bleaching:
Boiling water is used to remove sugars and fats, effectively destroying conditions suitable for insect survival; bamboo strips are placed in hot water at about 60°C, then 30% hydrogen peroxide (H2O2) and appropriate amounts of insect-resistant and mold-resistant agents are added in a ratio of 5% to 8%. The water is heated to boiling at 100°C using steam and maintained for 6 to 8 hours. For natural-color bamboo strips, an extra process which is bleaching with 90°C hydrogen peroxide for 4 hours.Carbonization:
The bamboo strips are placed in a high temperature, high humidity, and high-pressure carbonization pot, causing organic compounds such as sugars, starches, and proteins in the bamboo to decompose and denature. This process removes the nutritional sources for wood borers and molds, while also killing any insect eggs and fungi attached to the bamboo. After being subjected to high temperature and pressure, the bamboo strips turn a bronze or coffee-like color. The carbonization furnace pressure is 3Kg/cm2, maintained for 70 to 90 minutes.Drying:
The strips are then kiln-dried under 12% to remove excess moisture. Ensuring the bamboo is properly dry is critical to prevent warping or shrinking after installation.Pressing:
The strips are placed in a 900-ton press, where they are formed within 15 minutes. This process forms a rough block of solid bamboo. In a horizontal arrangement, the strips are placed flat, showcasing the bamboo's knuckles for a traditional look. In a vertical arrangement, the strips are stood on their sides creating a narrow, linear appearance.Trimming:
The rough edges and burrs of flooring planks need to be trimmed off then the milling of can go very precisely.Sanding:
The flooring boards are sanded flat and polished using a Dutch Sandmaster sanding machine.Milling:
This step includes cutting the bamboo block into the desired board width and length, as well as tongue-and-groove milling for the edges to ensure a secure fit during the installation process. We use the German-imported HOMAG machine for production, where only precise equipment can produce high-quality flooring.Painting:
The milled planks are then sanded for smoothness and finished with a top coat to protect the flooring from scratches, UV rays, and water damage. The topcoat typically consists of several layers of an aluminum oxide.Color Sorting and Packing:
The flooring has different color tones, so we will sort out all floorings by Dark, Medium and Light and pack in different cartons with noticeable marks.Big Stock:
We always carry big stock of flooring, the delivery time is within 3-10 days depending on your quantity.
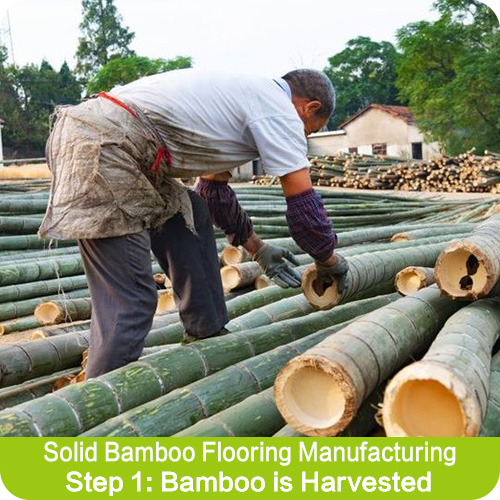
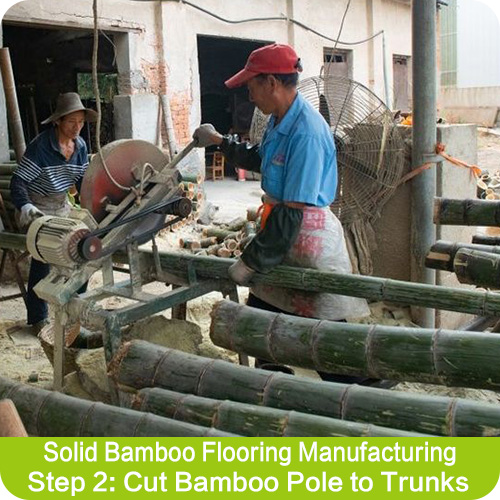
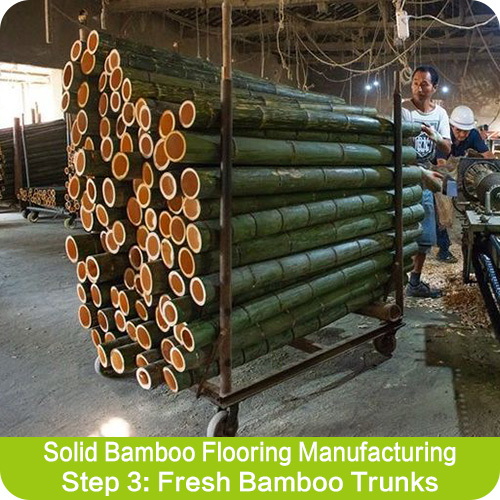
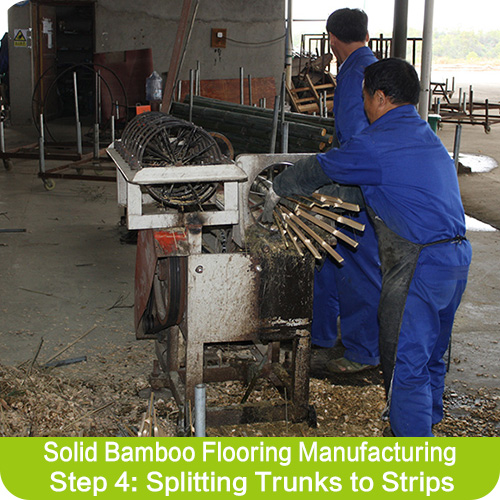
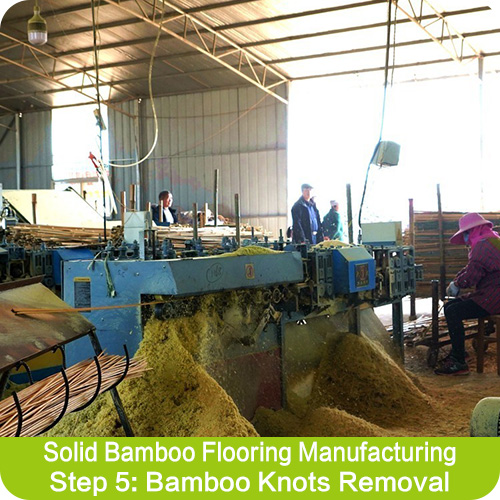
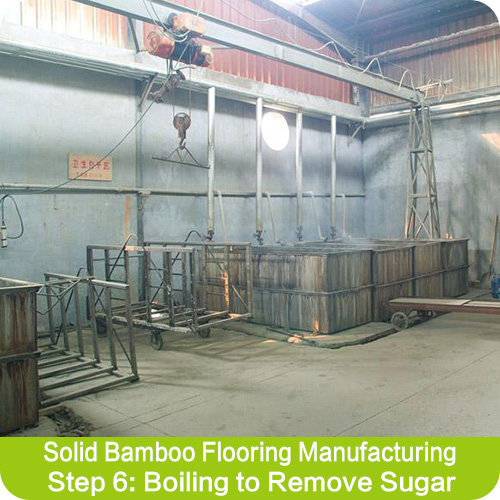
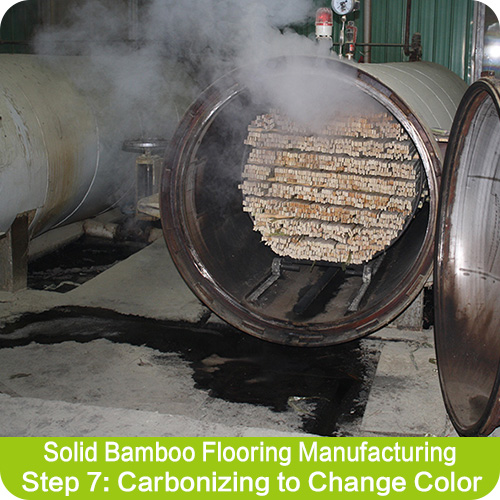
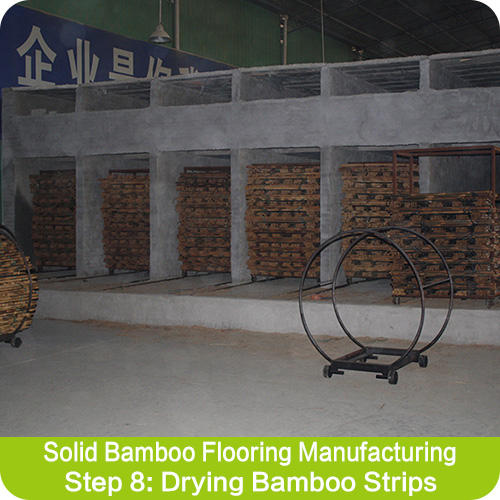
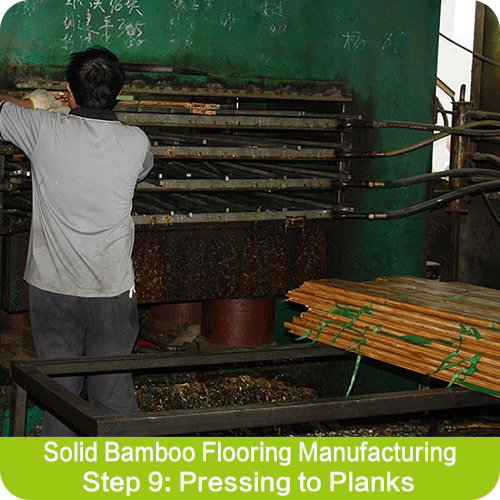
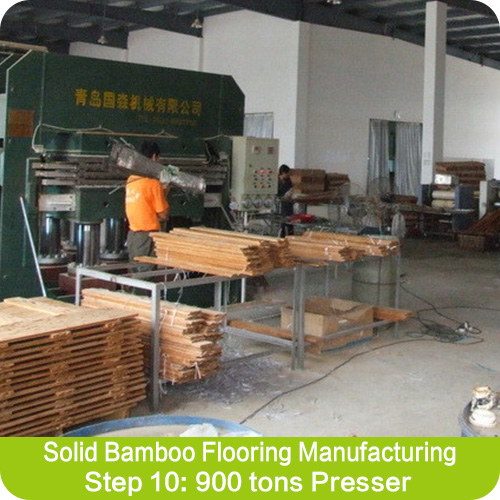
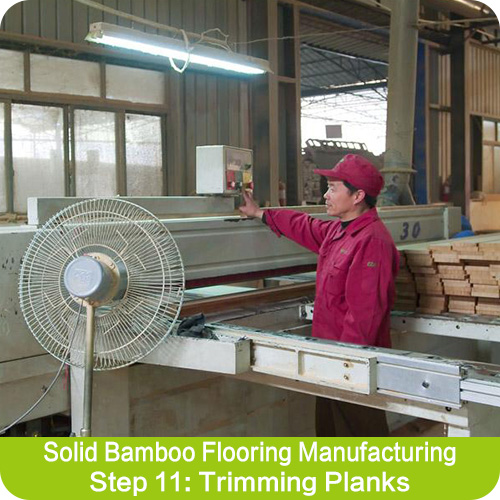
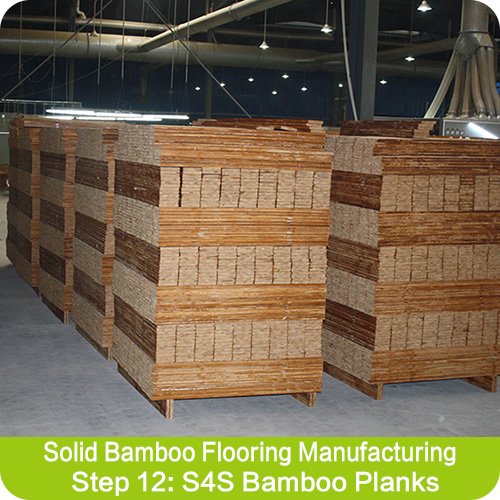
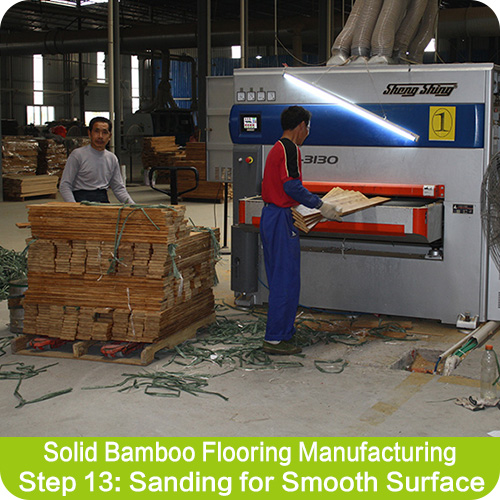
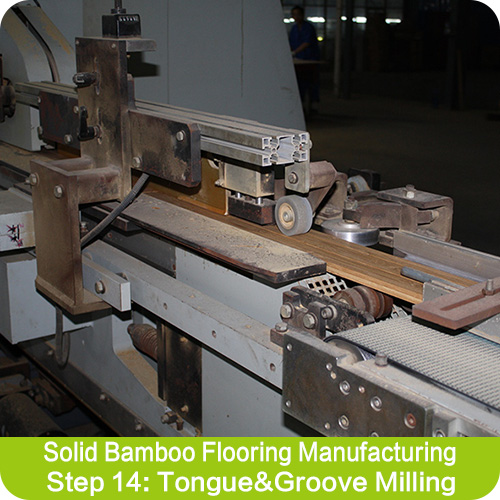
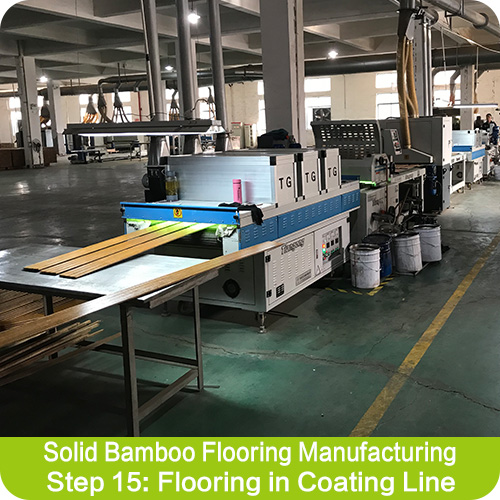
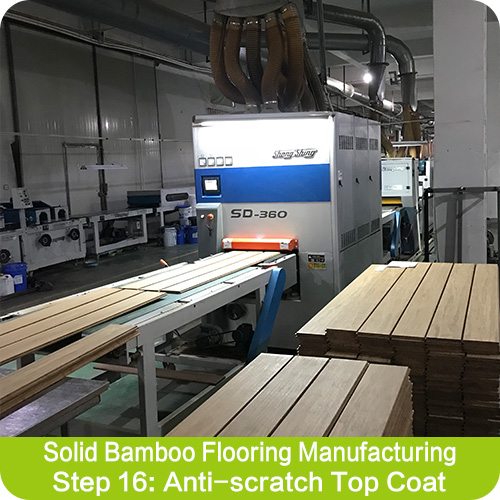
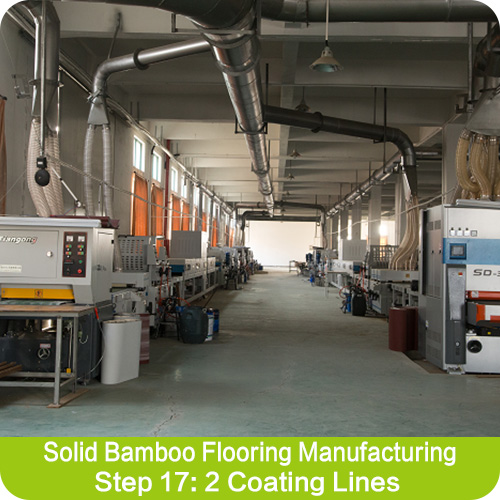
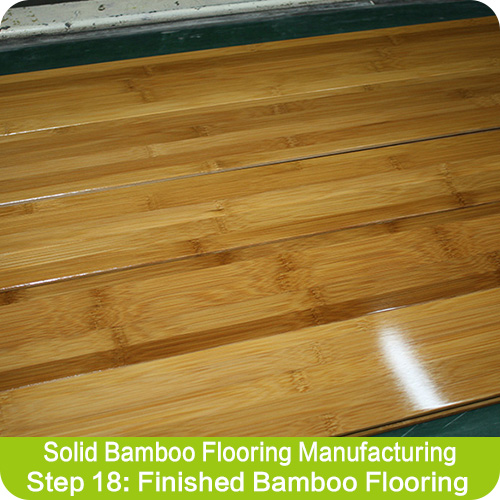
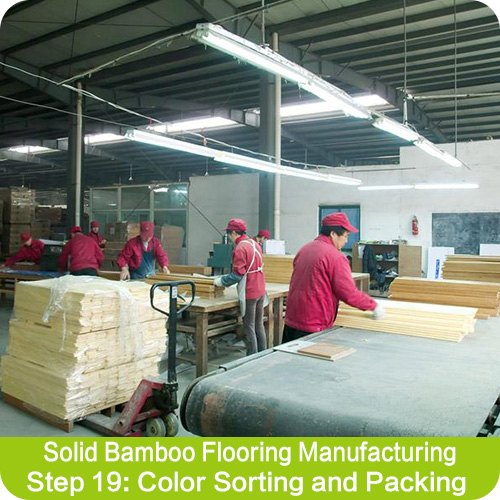
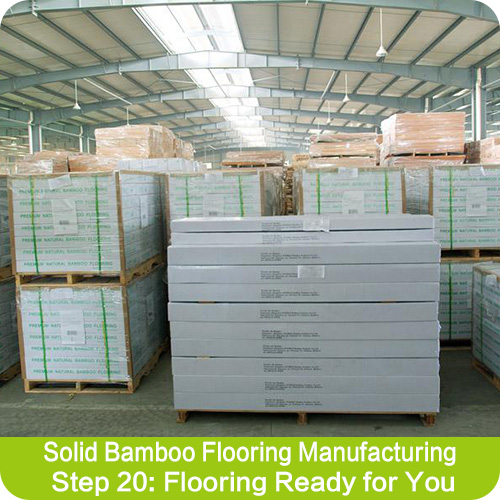
When it comes to selecting solid bamboo flooring, it's critical to assess both the quality of the product and the reputation of the manufacturer, as these factors significantly influence the flooring installed in your house for next 15-20 years.