How to Produce Strand Woven Bamboo Flooring
Strand woven bamboo flooring is a type of flooring made from bamboo fibers that are compressed under high pressure to create a dense, durable plank. Strand woven bamboo flooring offers a sustainable, durable, and attractive option for both residential and commercial spaces. Strand woven bamboo flooring is renowned for its exceptional durability and unique aesthetic appeal. Its manufacturing process significantly differs from traditional bamboo flooring, making it one of the hardest wood flooring options available.
Raw Material:
The primary raw material for strand woven bamboo flooring is bamboo, specifically the Moso variety, which is harvested at its peak growth of 5 to 6 years to ensure optimal strength and hardness. It has high density, strong resilience, and uniform color. The diameter is more than 6CM, and the bamboo thickness exceeds 3CM.Splitting:
Use a splitter to split the round bamboo tube to get bamboo strips of roughly the same width.Shredding:
Unlike traditional bamboo flooring, which uses strips of bamboo, strand woven bamboo flooring requires the bamboo to be shredded into fibers. This shredding process breaks down the bamboo strips into strands, which are then cleaned and dried.Boiling:
The bamboo strands are boiled in a solution of boric acid or lime to remove the sugar and starch, the addition of oxidized bleach and insect and mold prevention agents, will cause the soluble organic matter in the bamboo to settle out, killing any eggs and mold.Carbonizing:
To achieve a darker color, the strips can undergo carbonization, where they are steamed under controlled pressure and temperature.Drying:
After steaming and carbonization, the moisture content of the bamboo strips exceeds 80%, and it must be dried to control the moisture content below 10%. Natural color bamboo strands should be naturally dried at a low temperature if possible, to prevent secondary carbonization, causing changes in natural color. Bamboo strands will go through a drying tunnel.Soaking Glue:
All bamboo strands are mixed with a NAUF resin adhesive that is healthy adhesive guaranteed. When pressing, we will weigh the bamboo strands first before putting strands into the press machine, this will ensure the density of flooring.Compressing:
The press machine has a pressure of 2800 tons and a pressure of 0.19Mpa per square centimeter, to ensure a density above 1100kg/m3. Under intense pressure and heat, these strands are compressed together. The high pressure ensures that the strands are tightly bound, and the heat activates the adhesive, ensuring a solid block forms. This compression process enhances the hardness and density of the material, distinguishing strand woven bamboo flooring for its superior strength and durability.Curing:
The compressed blocks are cured in a kiln to harden the adhesive and ensure stability in the flooring product. This process also reduces the moisture content, preventing warping and expansion after installation. The curing temperature for natural color is 125℃ and 130~133℃ for carbonized color.Mold Unfolding:
This step includes cutting the bamboo block into the desired board width and length, as well as tongue-and-groove milling for the edges to ensure a secure fit during the installation process. We use the German-imported HOMAG machine for production, where only precise equipment can produce high-quality flooring.Trimming and Slicing:
The worker will trim off the rough edges, redundant length and width, and then slice the block into flooring – a fixed and desired size of plank.Sanding:
Sand the board before milling and painting to ensure the effect of the paint surface.Milling:
The milling machine is Homag which was imported from Germany, it can ensure the precision of tongue and groove, also click lock, the mill is more precise, the installation is more easy.Finishing:
Flooring will be applied with 7 layers of a UV-resistant finish to protect the floor from fading and wear. Advanced and stable quality of anti-scratch coating can enhance the flooring's durability further. This finishing process not only protects the floor but also gives it a polished, appealing look.QC and Packing:
The finished flooring will pass through a stringent quality control process where they are checked for defects, color consistency, and dimensional accuracy. Once approved, they are packed by cartons and on pallets.
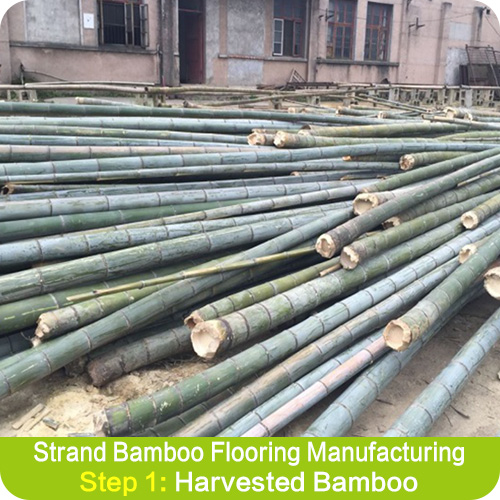
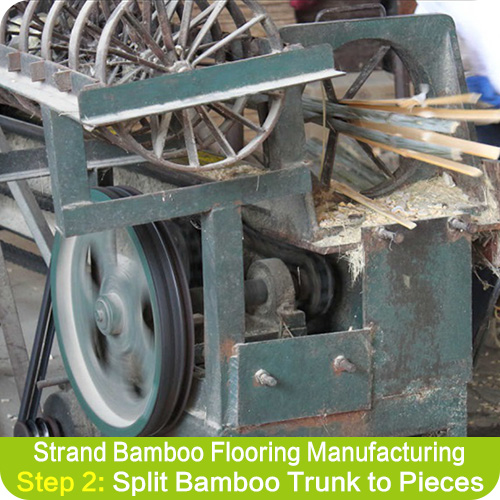
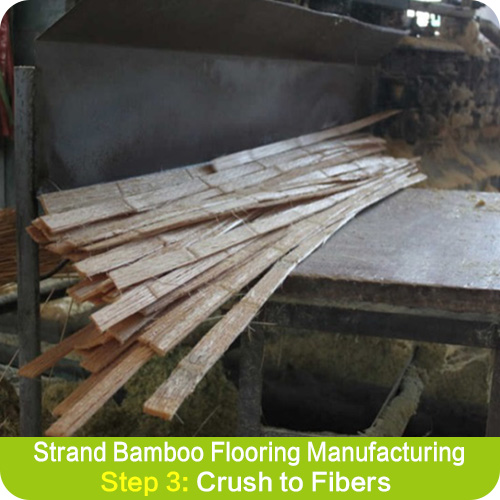
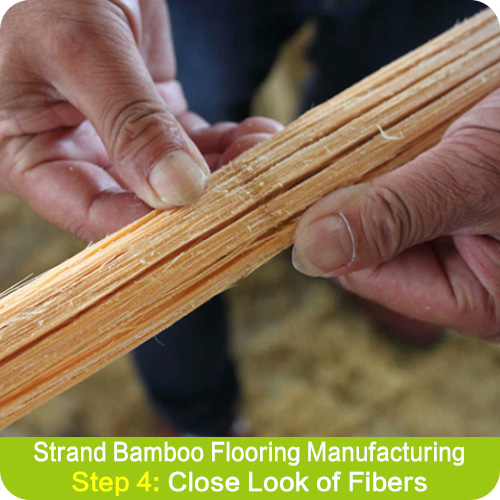
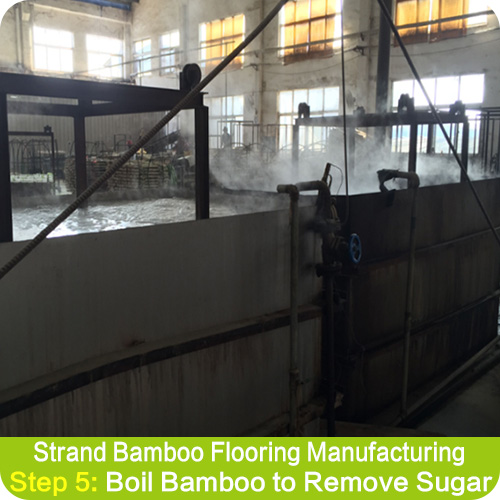
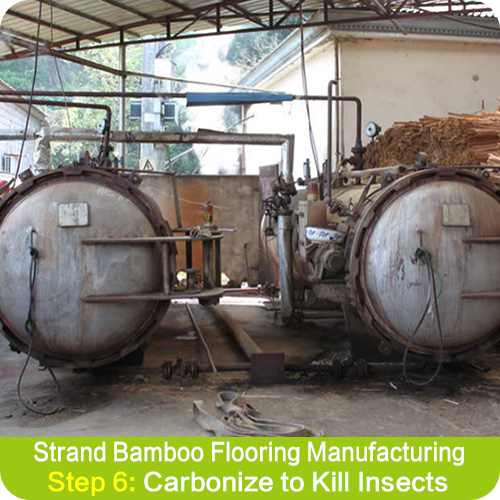
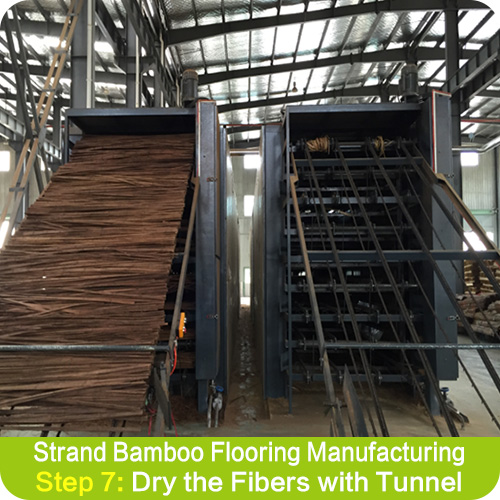
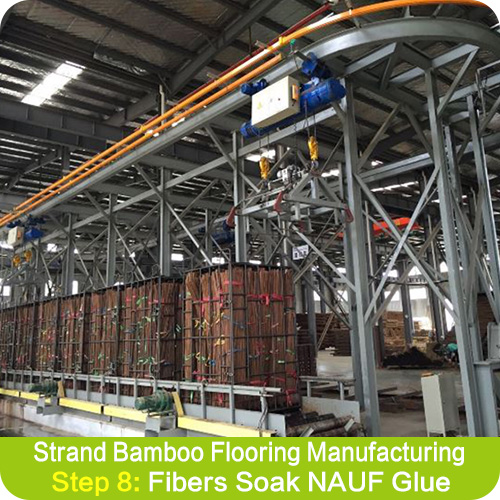
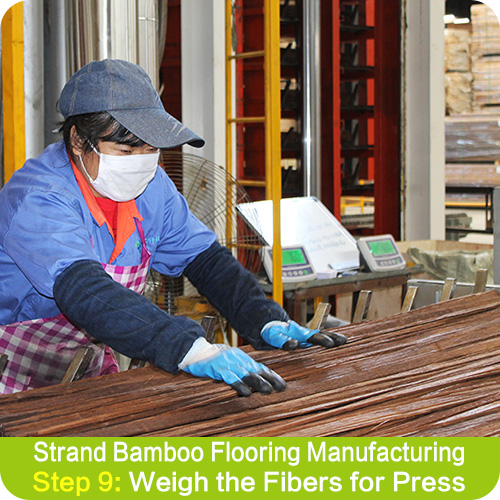
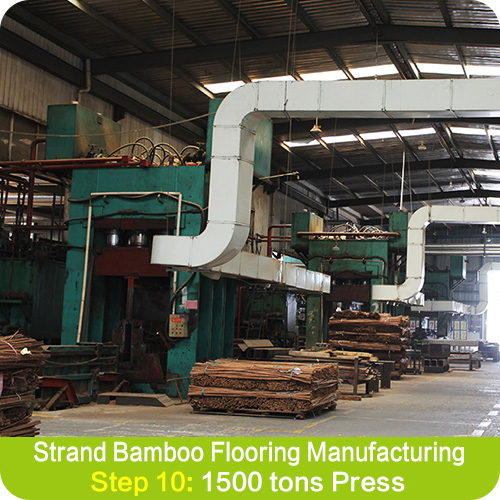
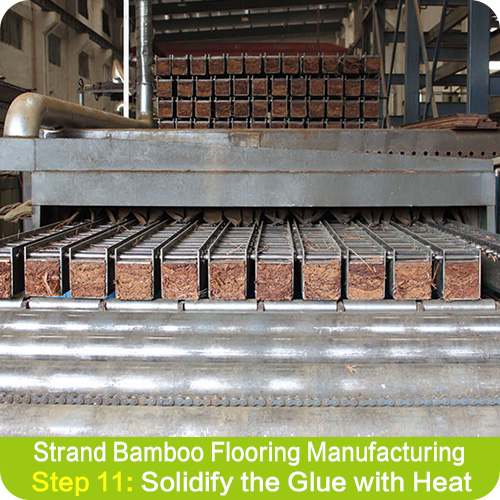
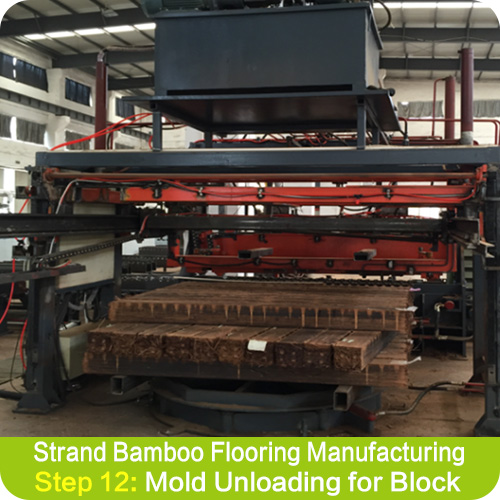
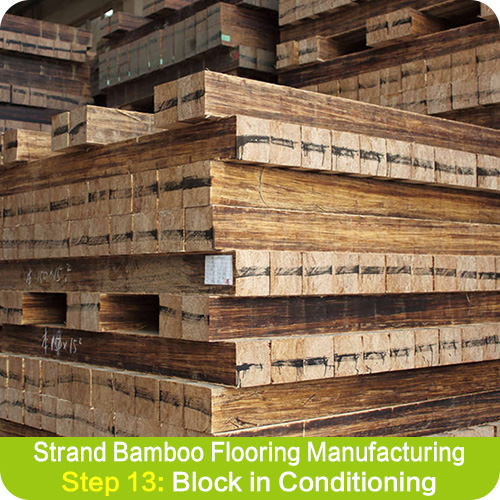
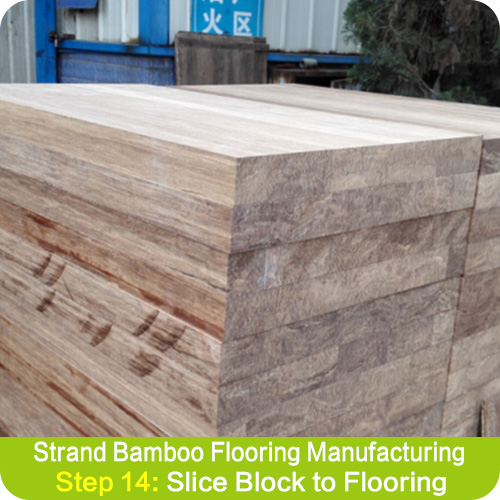
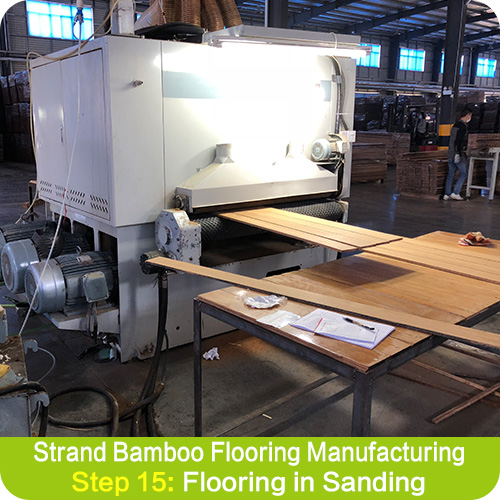
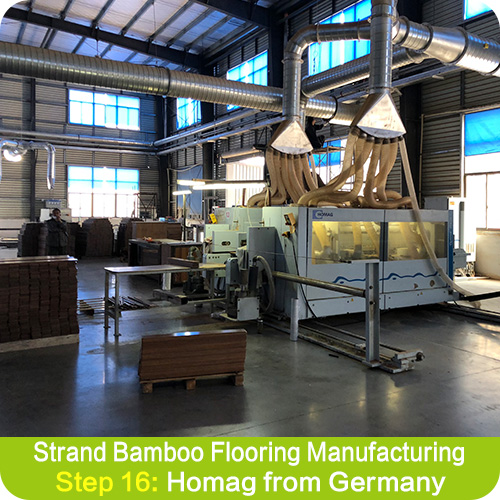
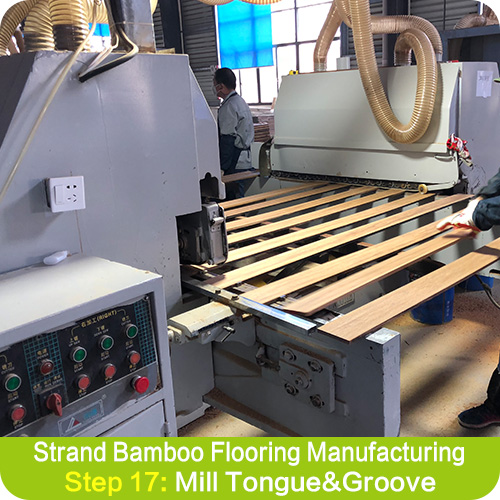
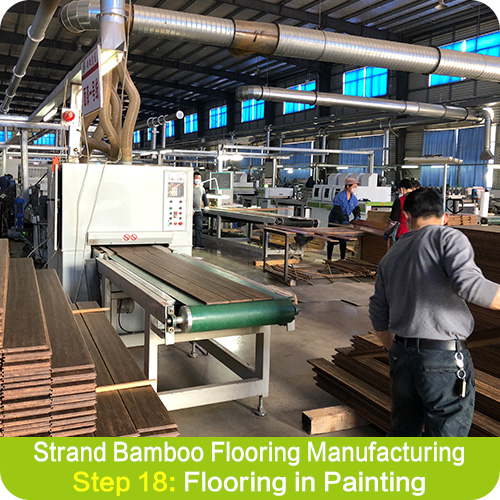
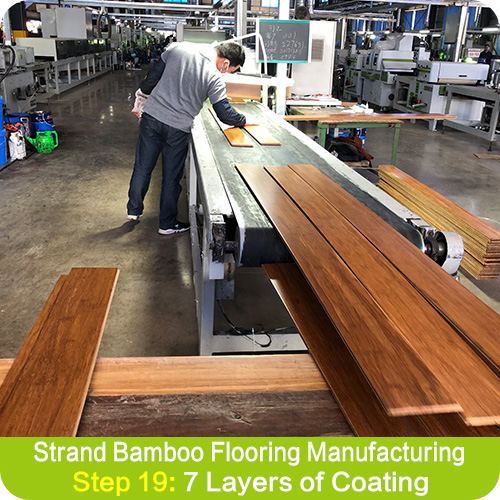
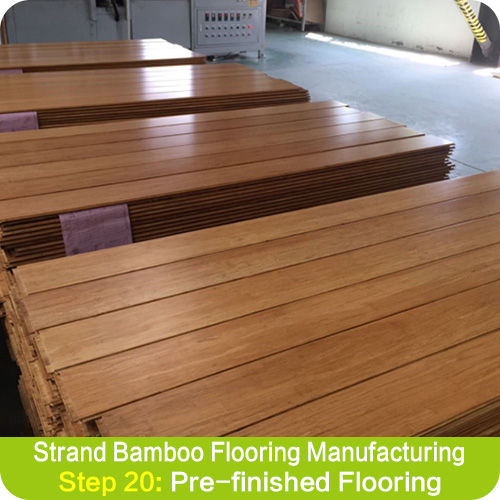
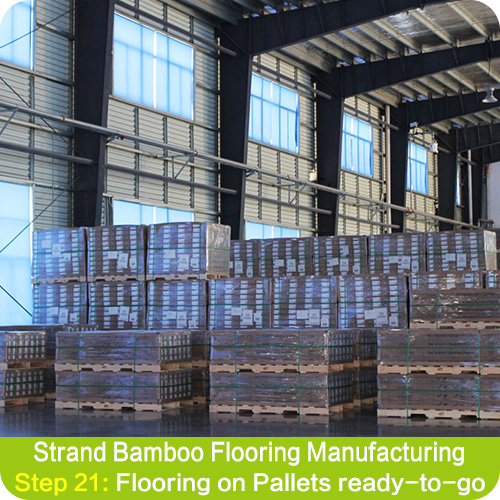
Strand woven bamboo flooring is considered an eco-friendly product due to the sustainability of bamboo. The resins used are typically low in volatile organic compounds (VOCs), making it a healthier choice for indoor environments.